My newest spinning and weaving project is calimanco, an 18th century fabric. The research journey has been documented in the German-language articles in this category, but since it proved rather difficult to find detailed information, I thought I should do my little bit to remedy that by sharing my findings with the international community.
When I learned that in the 18th century there had been damasks and even brocades made from wool, I was fascinated. I hadn’t thought it possible that damask, let alone brocade, could be made from anything else than silk. (Historically, of course. Forget about poly right this instant! Shoo!)
Well, ok, there’s linen, for household textiles, but those were more or less white and definitely not used for clothing.
Now I’ve inadvertently introduced the answer to the question that often crops up, „How on earth can wool, let alone that of those coarse longwool breeds, mimick silk?“ Simple answer: Colours. Both silk and wool are easy to dye with period dyestuffs, and keep the colours well. Linen and cotton are and do not. That’s basically it. With a non-crimpy, shiny wool and calendaring, you even get a sheen that would look almost, but not quite, entirely unlike that of silk. (I haven’t seen a freshly calendared period calimanco in person yet, though.)
Linda Baumgarten writes in What Clothes Reveal, “Colorful calimancoes that had been glazed mimicked more expensive silks, yet their long-lasting worsted fiber content was appropriate for a workingwoman’s garment.??? (p. 114) There’s a picture of a striped and a brocaded worsted fabric on the same page.
As long as I don’t own a drawloom, a damask or even brocade is unattainable, but the Nordiska Museet also has a multitude of samples of striped worsted fabrics that seem doable. I found a name for that type of fabric: calimanco. Here’s what they look like:
You can find more of them by accessing digitaltmuseum.se and searching for the words „tygprovsamling, Anders Berch, ylle“ or with the accession number in the above images.
Terminology
Textile fanciers who are at home in the English language or on Ravelry may be confused by the term worsted because it can refer to a yarn weight between DK and Aran. However, that’s far from what we’re dealing with here. Worsted, in this context, refers to the way the wool is prepared for spinning, and the spinning process that goes with it: The wool is combed, then spun in a short draw, resulting in a smooth, hard yarn – as opposed to woolen-spun, where the wool is carded and spun in a long draw, resulting in a lofty, airy yarn.
The fabric woven from such a worsted-spun yarn is also referred to as a worsted. The worsted class of fabrics contains various weaves besides calimancoes and damasks, e.g. crepe, serge and shalloon. Business suits are a typical modern application for worsted fabrics.
Early in my research I had encountered sources that mentioned wool damasks on the one hand while referring to the striped worsteds as calimanco on the other, hence the name of this project. Other sources mention solid-coloured, striped, damasked or brocaded calimancoes, including the contemporary texts quoted in Florence M. Montgomery, Textiles in America 1650-1870, and various German texts.
Calimanco can also appear as callimanco or calamanco in English, calamandre in French, Kalamank, Kalmang, Kalmank in German, calmink in Swedish.
For the scope of this project, the term calimanco shall refer to the striped kind only. The other ones shall be wool satin, wool damask or wool brocade.
The raw material
As has been mentioned, the wool has to be combed. Combing requires a certain staple (fibre) length. Quoth John Luccock in The nature and properties of wool : illustrated, with a description of the English fleece, 1805:
“The length of pile suited to the comb is upwards of four inches. The hose trade requires a considerable share of that which measures from four inches to eight, and the longer kind is usually destined to the fabrication of worsted yarn…??? (S. 155)
Few sheep breeds nowadays yield wool of that length. Fewer still are available commercially, prepared ready for spinning. (I’ve decided that spinning, dyeing and weaving are quite enough work besides a full-time day job without sourcing and preparing raw fleece as well.)
For a while I thought that only English breeds fit the bill because worsteds were only produced in England, specifically the Norwich region, but then I learned that there had been a healthy worsted trade going on in France and Saxony as well, and who knows where else. Still, the only suitable non-English breed I could find was the Dutch Texel, and that’s probably only because it was crossed with English longwool sheep in the 19th century. The Swedish Gotland would probably also be suitable, but I haven’t been able to source the white variety in a good enough quality.
These are the breeds that I tested: Devon,
Lincoln, Romney, Teeswater, Texel, Wensleydale, Perendale. Some people, when asked for recommendations, mentioned Bluefaced Leicester (BFL for short), but I know from previous experience that it’s too fine and short. Maybe they were mixing it up with Leicester Longwool which, unfortunately, isn’t available commercially.
from bottom: Teeswater,Texel, Wensley from bottom: Devon, Lincoln, Romney
After test-spinning various breeds, I found that there can be huge differences in quality, depending on the supplier. Teeswater was the longest and a nice spin. Together with Wensleydale and Texel, it forms a group of very similar, long, middling soft, but rather yellowish fibres. Devon is out on account of being way too coarse, closely followed by Lincoln. Perendale would be ok but is from New Zealand, i.e. not a breed used in European 18th century weaving. On top of being too yellow, Wensleydale and Texel are also not contemporary – Wensleys were first bred in the 19th century, and Texels appear to have acquired longwool properties no earlier than the 19th century.
What’s left is Kent Romney, mentioned by Mr Luccock as one of the 18th century longwool sheep. I had two samples from two different suppliers. One of them was definitely a longwool, i.e. not too fine, not too crimpy, but just above 20 cm in length. The other was crimpier, finer, just under 20 cm, and closer to BFL.
And that’s the hair in the soup, quite literally: BFL or, as Mr Luccock called it, the Dishley. According to Wikipedia, the Dishley, the Blakewell sheep and Blueface Leicester are the same, developed by Robert Blakewell (1725-1795). According to Mr Luccock, it was crossed into almost all longwool breeds, and since his book was published in 1805, that must have happened in the 2nd half of the 18th century. The Dishley had finer, but also shorter wool than the traditional longwool sheep. There seems to be a trade-off between fineness (i.e. a smaller fibre diametre as expressed in micron) and length, so when the Dishley was crossed in, the wool of the longwool breeds changed; it became finer and shorter. It is therefore nigh impossible to tell whether any 21st century wool is similar to the 18th century longwools just because both are from a breed of the same name. That may be the reason why one of my Romney samples didn’t really feel like longwool.
Colours
One of the most striking features of striped calimanco is how colourful they are, and the gradient stripes. A wide blue stripe may be made up of up to 14 different shades, ranging from dark navy to the palest blue, then a white stripe, followed by another gradient from pale blue to dark navy. Even if each gradient is only counted as one colour, there can be up to seven or eight colours in one fabric.
I haven’t looked for any written sources on the dyestuffs used because I’m fairly confident that after a few years of reading up on and experimenting with contemporary dyes, I can tell what the yarns were dyed with:
The warm, carmine red was dyed with madder, the cold, purplish red with cochineal.
Blue was dyed with indigo, either from the Indian Indigofera tinctoria or the European Isatis tinctoria.
A lot of plants yield yellow, but the most lightfast one was derived from Reseda luteola.
The hue of the brown stripes suggests walnut husks.
I have found two different types of green: An olive hue, as created by a yellow dye and iron additive (easy to achieve but rare in the swatches), and a brilliant green that could only be achieved by dyeing the yarn yellow and overdyeing with blue, or the other way around. Creating a smooth gradient of brilliant, double-dyed green requires great skill, emphasising the fact that the worsted trade was done on an industrial scale, with professionals on all levels, from the sheep breeders via the combers, spinners and dyers up to the weavers.
Number of Plies
I’ve tried to zoom in to the samples at the Nordiska Museet as far as possible, and came away with the impression that both warp and weft were unplied, single yarns. One has to look at the unravelled threads.
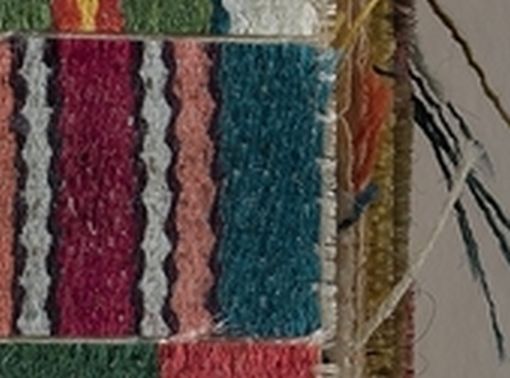
Then I trawled Google Books and found roughly contemporary books that said that the warp was 2-ply, the weft 1ply:
- Peter Nath. Sprengels Handwerke und Künste in Tabellen : Die Woll- und Seidenfabriken. Berlin: Verlag der Buchhandlung der Realschule, 1776 (p. 30, p. 97f)
- Johann Christian Schedels neues und vollständiges Waaren-Lexikon, Offenbach: Weiß und Brede, 1789 (p. 527)
Only one source suggests, indirectly, that calimancoes, at least English ones, may have been woven with a 1ply warp:
Russels, a kind of lasting, manufactured of double warp and single weft, and with a ???ve heald twill like the calimanco which it resembled in all respects except being stouter, having a double warp.
(John James, History of the worsted manufacture in England, London: Longman, Brown, Green, Longmans, & Roberts,1857, p. 362)
I am wondering whether the German sources that mention plied warp are reflecting a regional difference in how worsteds were made.
The Weave
There has been much confusion about the weave because the written sources contradict the extant samples I’ve seen, and one source even contradicts itself.
Judging from the samples at Nordiska Museet, I thought the weave must be a 5-shaft satin. Then I found written sources that all said that that striped calimancoes were 5-shaft twills:
- Peter Nath. Sprengels Handwerke und Künste in Tabellen : Die Woll- und Seidenfabriken. Berlin: Verlag der Buchhandlung der Realschule, 1776 (p. 84 & draft in appendix)
- G.P.H. Norrmann, Vollständigeres Wörterbuch der Produkten- und Waarenkunde, Hamburg: Carl Ernst Bohm, 1805 (p. 915)
- Pilo Blakeman, The Weaver’s Assistant, explaining in a familar manner, the first principles of the art of weaving. Bridgeport: N.L. Skinner, 1818 (p. 23)
- John James, History of the worsted manufacture in England, London: Longman, Brown, Green, Longmans, & Roberts,1857 (p. 362)
Sprengel and Blakeman each also published a draft:
Sprengel Blakeman
The Sprengel draft is a 5 shaft satin, despite the accompanying text saying it was a twill. The Blakeman draft is a broken 5-shaft twill.
I have compared the three different possibilities that the sources suggest – an unspecified 4/1 twill (Norrmann, James) which I interpret, for the sake of argument, as a straight twill, a broken twill (Blakeman draft) and a 5-shaft satin (Sprengel draft) – using my weaving software, iWeave, and a colour gradient that is typical of calimanco.
normal twill broken twill 5-shaft atlas
It seems obvious to me that the 5-shaft satin yields the smoothest warp stripe, the one most like the samples at the Nordiska Museet. You can’t see it in the above images, but if you add stripes that are only two ends wide, you get the same wavy stripes as in the Nordiska Museet samples only with the satin tie-up.
P.S. Following a recommendation on Ravelry, I have bought a book that cinched the weave question even before I read a single word. There was a picture on the cover that wasn’t much clearer than the ones from the Nordiska Museet, but the weaver was kind enough to include a stripe of alternating yellow and green warp threads, with a weft of red. The contrast made counting easier, and it was – drumroll please – a 5 end satin.
Addendum: The twill vs satin question has meanwhile been answered by contemporary weaving books. While modern weavers distinguish between plain/linen weave, twill and satin/atlas, the 18th century textile trade distinguished between plain, twill and flowered, and the texts make it clear that there is no distinction made between twill and satin. Sources:
- Peter Nath. Sprengels Handwerke und Künste in Tabellen : Die Woll- und Seidenfabriken. Berlin: Verlag der Buchhandlung der Realschule, 1776, p. 69
- Joh. Heinrich Moritz Poppe, Technologisches Lexicon. Dritter Theil H-M. Stuttgardt und Tübingen: J.G. Cotta’sche Buchhandlung, 1818, p. 227
- Pilo Blakeman, The Weaver’s Assistant, explaining in a familar manner, the first principles of the art of weaving. Bridgeport: N.L. Skinner, 1818, p.1
Open Questions
Some sources say the warp was 2ply, one suggests 1ply. Are both historically correct?
What is the usual yarn gauge? (i.e. thickness of the yarn)
What is the usual sett? (i.e. how many warp ends per centimetre)
3 Antworten auf The Calimanco Project